NATURAL GAS ENGINE LUBRICATION
Maximize The Efficiency & Minimize Maintenance Costs
Steel Shield Gas Engine Oils provide outstanding protections against nitration, oxidiations and other adverse effects during operations and downtimes. The ABF Technology performs continuous treatments on the metal, not the oil, to make any motion ultra-smooth without any hidden side-effects. It is definitly the most powerful lubrication technology in the world.
Natural gas engines (NGE) are used to power natural gas compressors, electric generators, fire water and irrigation pumps, etc. They are also commonly used to generate electricity in primary cogeneration power stations. Natural gas engines generate less NOx, CO and other particulates than diesel engines, and may induce lower fuel costs in some applications. The major characteristics of natural gas engines are as follow:
- Use 2 or 4 stroke
- Designed power range: <100 to 16,000 HP (800 to 1,500 HP are the most common)
- 1 to 20 power cylinders
- Oil sump capacities of 14 to 6,000 litres (300 to 800 L are the most common)
- Engine speed: From 300 RPM (low speed) to 2,000 RPM (high speed). Over 80% of all engines are running more than 800 RPM
- Piston bores sizes: 22.5 inch (572 mm) in low speed units, 3.5 to 9.45 inch (89 to 240 mm) commonly used in high speed units
- Inlet air: Naturally aspirated or turbocharged (⅔ of new engines are turbocharged)
- Stoichiometric or Lean Burn (a relative term for an air / fuel ratio higher than stoichiometric) to reduce NOx emissions
- Engines and compressor units can be either "separates" (joined end to end at the crankshaft by a coupling), or "integrals" (engine and compressor have a single common crankcase)
Typically, the fuel in natural gas engines is sweet, dry natural gas ("sale gas" with >85% methane). Sometimes, in the gas production fields, raw sour natural gas having H2S (up to 8,000 ppm), carbon dioxide and nitrogen is used. Also, digester gas collected from sewage systems and landfill gas are becoming more commonly used as fuels. However, their qualities are very poor due to lower methane content (50%) and commonly contain silicon based compounds, such as flourides, chlorides, copper, tin, iron, hydrogen suphide and carbon dioxide (up to 50%). Those substances can cause adverse effects to the engine because they can turn to high corrosive and abrasive substances, and the energy content is low.
Natural Gas Engine Lubricants
The chemical formulations of natural gas engine lubricants are differet from diesel and gasoline engines, because natural gas engines:
- Burn cleaner: No soot contamination of the crankcase engine oil. The ash contents can be lowered, and lower detergency and dispersancy are needed
- Burn gasous fuel: No fuel dilution. Avoiding the viscosity increase of the lubricant becomes a major concern
- Constant speed operation: Problems of deposits accumulations and plug fouling are more serious
- Some engines burn at higher temperature (e.g. 165 to 235℃ exhaust temperature) than diesel: Oxidation and nitration of lubricants are increased as is valve wear
Multigrade NGEO (Natural gas engine oils) provide good low temperature "cold-start" ability for the engines while lowering fuel consumption, emissions and increasing fuel economy. But they may trend to increase the nitration of the lubricant. Also, notice that NGEO do not have API (American Petroleum Institute) minimum performance designations as are common with diesel and gasoline engine lubricants (e.g. CJ-4, SM). Majority of the natural gas engine manufacturers specifiy oil by the properties of the oil. Some engine makers established their own natural gas engine tests, but field tests are the most typical methods to evaluate component performance. Dresser-Rand and Waukesha cogeneration applications have the only 2 published approval lists for brands of the oils. There has been discussions about developing API NGEO performance designations since the late 1980's but it has not occured. Therefore, natural gas engine users must depend on the integrity of the lubricant supplier to provide high quality lubricants.
Most of the OEM gas engine oils provided by the engine manufacturers do not disclose the contains of the additives. The performance of those lubricants are totally unknown. The most important point is there exist better lubricants in the market. Steel Shield Gas Engine Oils have much better lubrication technology than the others. Once the users try, they will see the difference very soon.
Ash Content Of Natural Gas Engine Oil
Ash is the portion of the lubricant which left as a deposit after it completely burned. It is in white-gray colour which creates by metallic detergents (calcium, barium and magnesium) and anti-wear (zinc and phosphorous) additives. The ash content is defined as four levels:
- Ashless: <0.1% sulphated ash
- Low Ash: 0.2-0.6%
- Medium Ash: 0.7-1.2%
- High Ash: >2%
Ash directly protects the valve in stroke engines while detergent additives (which are bases) neutralize acids. So, the lubricant with the lowest ash content which provides the most basic protection for the valves and neutralizes the acids is prefered. Please notice that, the higher the ash content, the more the deposits accumulated inside the engine. If an engine was found to have high deposit level, it might be caused by applying a lubricant with ash content higher than desired, or due to over lubrication, other mechanical factors, etc. These can lead to poor heat transfer, preignition, detonation, ring sticking or breaking, plug fouling and valve burning.
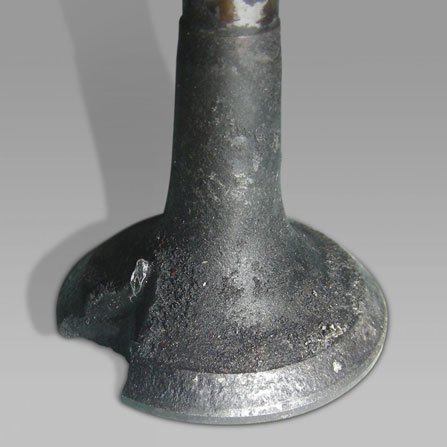
Fig.1 - Burnt (Torched, Guttered) Exhaust Valve
Low and medium ash content lubricants are commonly used in four stroke engines to prevent valve recession with a sacrificial protective ash layer forming on the exhaust valve and seats. High ash content lubricants are only used in older Waukesha four stroke engines because of their 45° high valve angles. Higher ash content lubricants with high Base Numbers are required to neutralize highly corrosive fuels. Ashless lubricants are generally used in two stroke engines (usually have large bore cylinders and have oil injection ports feeding lubricant into the cylinder directly) without intake or exhaust valves to reduce exhaust port blockage. Low ash content lubricants are the most typical and best choice for various types of engines which supplied from one lubricant tank.
Exhaust valve recession and torching (guttering) are common engine problems which are wearing of valve sealing face caused by the valve's continuous and unprotected closing motions. The problem leads to damages of the valve and the insert seat in the head. Insufficient ash content / issues in ash compositions in the lubricant or inadequate oil feed to the valve stem can lead to these problems.
Steel Shield Gas Engine lubricants have high quality ash composition and carefully controlled ash contents together with unique ABF Technology. They can definitly protect valves from guttering and torching, and prevent valve recession.
Nitration Of Lubricants
Nitration is a degradation of lubricant caused by chemical reaction between gaseous nitrogen oxide (NOX) and the lubricant under combustion process. It is related to air-fuel ratio, peak combustion temperatures, engine RPM, engine spark timing, loading and ambient air conditions. NOX is also the major pollutant of gas engines. The higher the combustion temperature, the more the NOX created. In order to reduce the NOX content, additional air must be forced into the lean burn engine which is similar to exhaust gas recirculation (EGR) in diesel engines.
The NOX gases can react with the lubricant film on the cylinder wall or crankcase sump after leaving the combustion chamber, and then turn into complex liquid nitration products.
Nowadays, the reactions in the lubricant which lead to nitration are still not thoroughly understood, and they are different from the oxidation process. Nitration of the lubricant is mainly affected by:
- Exhaust gas scavenging efficiency (exhaust gas removal from the combustion chamber): If this efficiency enhanced, reactions between NOX and the lubricant reduced, and the rate of nitration also droped
- Cylinder wall temperature: When the temperature of the cylinder wall reaches 150℃, the liquid nitration products will be destroyed apparently. So, low cylinder temperature can lead to nitration which are more common in low speed and naturally aspirated four stroke engines
- Piston ring efficiency: The higher the blow-by reduction, the lower the NOX interacts with the lubricant to form nitration products
- Crankcase ventilation: The better the ventilation, the lower the nitration products (the same advantage as the exhaust gas scavenging efficiency)
- Oil sump temperature: When the temperature of the oil sump temperature approach 70℃ and below 80℃, nitration caused by the reaction between the blow-by gases and the oil increases (This is different from oxidation in which oxidation rate increases significantly above 90℃ and increases with temperature)
- Base oil type: Some base oil types, lubricant with lower viscosity base oils, lower viscosity index improver additives of multigrade oils are trend to nitration. Base oils with saturated hydrocarbon structures, like PAO synthetics and hydrotreated paraffinic oils are less trend to nitration
Nitration in the lubricants can lead to severe results:
- Viscosity inrease
- Lubricant acidity increase
- Lubricant solubility decrease: results in varnish formations in hot locations of the engine which sticken the ring, and sludge accumulationss in cooler location of the engine which plug the filter.
Nitration generally cause risks in older, lower speed, stoichiometric four stroke engines. However, two stroke engines which significant lubricant contents removed from the crankcase and fed to the combustion cylinder oil injection system primarily do not have nitration problem. It is because majority of the nitration products are being removed from the exhaust ports, and the fresh lubricant to the crankcase increases.
Notice that there is NO additives known can be formulated to the lubricant to inhibit the nitration process. Nowadays, nitration can only be controlled by the selection of nitration resistant components in the lubricant. Steel Shield Gas Engine lubricants are always the right choice to achieve low NOX contents.
Lubricant Change Frequencies, Drain Intervals
These frequencies are recommended by the engine manufactureres. The drain intervals can be reduced by using low quality fuels and other mechanical factors such as poor fitration, high loadings, etc. In order to extend lubricant intervals, good maintenance practice should be required, and proper used oil analysis is necessary. Tests like FTIR (Infrared) can monitor oxidation and nitration; BN (Base Number) can monitor detergency additive depletion from acids neutralizing the reserve alkalinity; AND (Acid Number) can monitor the content of organic acids; Standard spectrographic analysis can monitor wear metals. Over extended lubricant drains and inadequate filtration cause engine damages and degradions in both metal and oil, and finially lead to short engine life.
However, if lubricant change too frequent, it will induce high lubricant cost and high downtime costs which can be a huge figure. Steel Shield provides users a optimium choice which can extend lubricant drain intervals and reduce engine downtimes. This can only be achieved by Steel Shield ABF Technology. Check our our Gas Engine lubricants and contact us for more details.
Catalyst Systems
Their functions are to minimize emissions in order to protect the environment. They have three categories: Non-Selective Catalytic Reduction (NSCR) system, Selective Catalyst Reduction (SCR) systems, and Oxidation Catalyst systems. Most catalyst element poisioning by phosphorous or zinc compounds, and ash content is a concern which related to the lubricant. Therefore, some catalystmanufacturers set limits on those compounds and oil consumptions.