REFRIGERATION GENERAL KNOWLEDGE
The Steel Shield EPA with ABF Technology is specially formulated to protect and prolong the life of the compressor unit and to restore the lost efficiency of the heat exchanger system due to fouling. This results in less maintenance and down time for HVAC&R equipment and reduces operating costs. STEEL SHIELD lubricants are completely inert relative to all refrigerants and their respective lubricants and will not affect filter performance in any way. Now, use STEEL SHIELD on your commercial and residential air conditioners, refrigeration systems, heat pumps, ammonia and non-ammonia systems.”
Types Of Refrigeration Systems
Unlike air-conditioners, The American Society of Heating, Refrigeration and Air-Conditioning Engineers defines a refrigeration system as any use of mechanical or absorption refrigeration machinery for applications other than the comfort of human being.
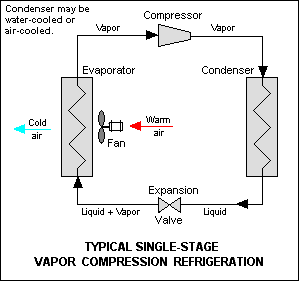
Either single stage or multi-stage multi-compressor systems can achieve refrigeration. The simple form of single stage system consists of a compressor, a condenser, an expansion valve and an evaporator. Firstly, the compressor compresses the gasous refrigerant to high pressure to become a semi gas-liquid mixture. The compressor is lubricated by the compressor lubricant. When the refrigerant passes throught the condenser, it is being converted to liquid when the high is removed by the mean of air-cooling. Then, when the liquid passes throught the expansion valve, the pressure decrease dramatically which leads to temperature drop as low as -20℃ or -30℃. The gasous mixture finally comes to the evaporator and absorbs heat from the surrounding. The cycle is then being continued and the refrigerant flows back to the compressor.
Types Of Compressors
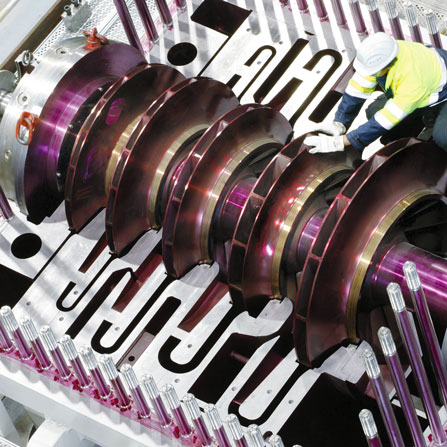
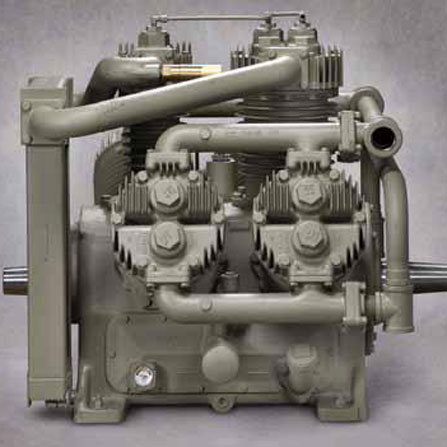
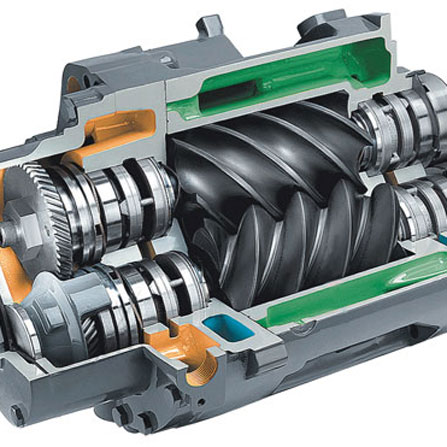
Centrifugal Compressor
Reciprocating Compressor
Rotary Screw Compressor
The three main types of compressor which require lubrication are centrifugal compressors, reciprocating compressors and rotary screw compressors. They are all facing the problems of boundary lubrication during cold-start / start-up and high-pressure operating situations. Also, hydrodynamic and elasto-hydrodynamic conditions are very common.
Centrifugal compressors include impeller and rotary vane compressors. The principle is to induce high gas pressure to create liquid flow. Many mechanical components require lubrication, such as shaft and bearings, seals, gear reducers and the rotor tip / ring interface. This type of compressors can allow lubricant to mix with refrigerant to lurbicate components.
The reciprocating type compressors have pistons, piston rings, cylinders, connecting rods bearings and wrist pins which require lubrications. They can be lubricated by simple oil splash, or more complex lubricant feed system.
Rotary screw compressors can be divided into wet type and dry type (oil free) which both consist of shaft and bearings, rotors and seals, and require lubrications. In wet types, lubricant is being pumped to bearings and seals while rotors can be cooled down and sealed by mixing the lubricant into the refrigerant. In the dry type compressor, only the gear system (timing gears) requires lubrication.
All types of compressors mentioned above need a lubricant seperator in the downstream to eliminate the oil droplets from the refrigerant flows.
The Selection Of Lubricants In Refrigeration System
Compatibility between the refrigerant and the lubricant (both mineral and synthetic) is a critical factor in the selection process. They are mixed together to achieve compressor lubrication, but the lubricant usually cannot be completely seperated from the refrigerant after compression. The typical types of refrigerants included: chlorofluorocarbons (CFC can cause damage to the ozone layer and thus being restricted), hydrochlorofluorocarbons (HCFC), hydrofluorocarbons (HFC), ammonia, carbon dioxide and hydrocarbons (e.g. propane, propylene, etc).
The following criterias need to be consider when choosing lubricants for a refrigeration system:
- Wear protection, sealing, dampening noise reduction, vibration reduction properties of lubricant
- Low temperature properties of the lubricant
- High temperature properties and thermal stability of the lubricant since the compression process can create temperature as high as 160℃
- The dielectric strength and the compability with electric motor parts, insulation and varnishes in the closed hermetic compressor system
- Lubricant and refrigerant compatibility, liquid-liquid miscibility and gas-liquid solubility
- The cleanliness of the refrigeration system, such as particulate and moisture contamination
Types Of The Lubricants
Refrigeration lubricants can be divided into paraffinic, naphthenic minerals oils and synthetic fluids.
Paraffinic oils have better thermal and chemical stability which are more resistant against ammonia effects. They are generally used with HCFC, ammonia and hydrocarbon refrigerants, and have good miscibility with HCFC and hydrocarbon gases. However, their cold flow and miscibility with other refrigerants are not ideal.
Naphthenic oils have better miscibility and pour point. They can be applied with HCFC and hydrocarbon refrigerants. Their lower wax contents makes them suitable in low temperature operations, but their thermal stability are poor.
Both paraffinic and naphthenic oils are not miscible with the new HFC refrigerants. Therefore, synthetic oils are used to overcome those problems and provide better miscibility, coking and waxing abilities. Synethetic refrigeration lubricants include:
- Polyalphaolefins: Can be choosen as a substitute of mineral oils in high stability or low pour point system requirements
- Alkylbenzene: Can be mixed with mineral oils to enhance miscibility with HCFC refrigerants in HCFC and ammonia refrigeration systems
- Polyol ester: Working with new R-134a lubricant, especially in automotive air-conditioners. Good for new HFC systems and suitable for HCFC systems, but not chemically incompatible with ammonia refrigerants
- Polyglycol synthetic lubricant: Working with new R-134a lubricant, especially in automotive air-conditioners.
The most common additives being used in refrigeration lubricants are: pour point depressants, floc point depressants, viscosity index (VI) improvers, thermal stability improvers, extreme pressure (EP) additives, rust & corrosion (R&O) inhibitors, anti-foam additives, metal deactivators and dispersants. However, the contents of the additives added should be as low as possible because they can have negative effects on thermal and chemical stability as they are reactive. The compatibility of the lubricants and refrigerants can be summarized as follows:
Refrigerant | Lubricant |
---|---|
CFC (Old type), e.g. R11, R12, R13 | Naphthenic Mineral Oil |
HCFC, e.g. R22 | Naphthenic Mineral Oil, Paraffinic Mineral Oil, Alkylbenzene Synthetic, PAO Synthetic, Alkylbenzene / Mineral Oil Mix, Polyol Ester Synthetic |
HFC, e.g. R134a | Polyal Ester Synthetic, PAF Synthetic |
Ammonia | Paraffinic Mineral Oil, PAO Synthetic, Alkylbenzene Synthetic |
Carbon Dioxide (CO2) | High Viscosity Mineral Oil |
Hydrocarbon (Propane) | Paraffinic Mineral Oil, Naphthenic Mineral Oil, PAG Synthetic, PAO Synthetic |
Table 1: Refrigerant / Lubricant Compability (Always follow the instruction made by OEM and the lubricant supplier)
Ref.: "Refrigeration System Lubrication" Basic Handbook of Lubrication. 3rd ed. USA: Society of Tribologists and Lubrication Engineers - Alberta Section, 2011. N. page. 184 Print.The Viscosity
The viscosity of the lubricant must be high enough to protect metal from wears. Another concern is the effect of the refrigerant fluid on the viscosity of the lubricant because the vapourized refrigerant can reduce the lubricant viscosity in the compressor. ISO 32 to ISO 68 are the most common viscosity range of refrigeration lubricants. ISO 22 and ISO 680 lubricants are required in some systems such as reciprocating compressors and twin rotary screw compressor respectively. Also, when temperature increases, the lubricant viscosity decreases. Therfore, in order to prevent wax formation in the evaporator (which is the section with the lowest temperature), the lubricants must have adequately low pour point.
To maximize the efficiency of the refrigeration system, the lubricant with the lowest possible viscosity should be applied. According to the ASHRAE System Handbook, it is recommended that to calculate the total volumetric efficiency of the system by applying different lubricants of various viscosity. It is suggested to select the lubricant which can achieve the best efficiency within a set of temperatures. The lowest required viscosity at the higest operation temperature should be taken into account as well. Also, the final viscosity changed by the dissolved refrigerant (in liquid and gas form) must be considered.
The viscosity index (VI) should be high enough as the refrigeration system runs at both high and low tempeatures. There is a necessary compromise between high VI (paraffinic) mineral lubricants and the low temperature flow, and refrigerant solubility properties of low VI naphthenes and aromatics. Therefore, more advanced synthetic lubricants with excellent low temperature fluidity, zero wax content, good solubility and high VI are becoming more and more common.
The Compatability Between Lubricant & Refrigerant
In the compressor, the lubricant in the refrigerant is the component which achieves lubrication. But in the rest of the system, the refrigerant is the main fluid doing heat exchanges. Lubricant and refrigerant are almost totally mixed in the wet screw compressor. In the majority of other compressor systems, lubricants remain in the refrigerants after leaving the compressor, then they flow to other area. This is the reason the refrigerant and the lubricant must be compatible.
Paraffinic lubricants provide better resistance than naphthenic and aromatic lubricants in thermal and chemical reactions. It is important that the lubricant must be inert after mixing with the refrigerant. The mixture should be able to resist the catalytic reaction creates by the presence of metal components under high temperatures. Lubricant degradation, carbon, sludge and varnish generations, gumming and copper plating on bearing surface can be caused by chemical incompatibility. Copper plating is generally a thin layer, it dissolves the copper from the tubings, then deposites on bearing surfaces, vanes or valves, and finally leads to mechanical failure. Copper plating is caused by the reactions of lubricant and refrigerant with the presence of water or other contaminations.
Excellent miscibility between lubricant and refrigerant under operation temperature and pressure is a highly optimum condition. It is known that the liquid or vapour refrigerant content in the lubricant depends on the liquid phase pressure, the gas pressure and the nature of either fluids. The final characteristics of the lubricant-refrigerant mixture must be considered because common CFC and HCFC have stable miscibilities with minerals oils, while ammonia, carbon dioxide and new ozone-friendly HFC (R134a) have poor mineral oil miscibilities. Also, the viscosity of the mixture might not be the hightest at the coldest locations of the system (evaporator) as the refrigerant content is usually high at those areas. Further more, the viscosity of the solution decreases after leaving the evaporator because the temperature increases and the refrigerant content decreases. In reality, vapour solubility in the lubricant is affecting the compressor noise dampening. This problem can be solved by the formation of moderate foam layers, however, too much foaming can resist heat removal and lubrication.
The final property need to be considered is the change of solubility of lubricant-refrigerant mixture: the refrigerant rich liquid and the oil rich liquid phases. In the compressor crankcase, the refrigerant rich layer can lead to lubricant starvation during system start up because it is denser and settles to the crankcase bottom. However, in the evaporator, the oil rich layer can lead to lubricant starvation and reduction in evaporation efficiency due to "oil-logged" caused by the collection of the oil rich portion in the location where the high velocity return gas flow does not reach.
The Lubricant Pour Point
Lubricants with low enough pour point should be selected, and it should be able to flow at the coldest areas of the system.
For those fluids which are completely immiscibile, the actual pour point becomes the key characteristic to be consider. It is because the lubricant is not virtually pure oil phase in the evaporator for those mixtures, such as "ammonia refrigerant - mineral oil" or "carbon dioxide refrigerant - mineral oil" mixtures.
For those fluids which are completely miscibile, the properties of the solution become the key area to concern. The floc point (the temperature which wax crystals are formed) of the mixture must be lower than the evaporator temperature in order to prevent wax crystal to form, and causes deposits and line blockage.
For those fluids which are partially miscibile, the phases of the mixture and thus the properties can be different at various locations. Therefore, both pour point and floc point can predict the characteristics actually, and the system must be carefully monitored.
The Compatibility of Lubricant And System Materials
Make sure that the lubricant compatible with the materials. It becomes critical when user decides to switch from one lubricant to another. For example, naphthenic oils can cause swelling of seals, while severely hydrocracked paraffinic materials or PAO lubricants can lead to shinking of seals. Some synthetic oils such as aromatic may not be compatible with seal and hose materials. Also, some of the lubricants can damage the insulations and varnishes installed in electic motors and hermetically sealed systems.
The Volatility of Lubricant
Lubricants with low volatilities can be carbonized and reduces flash points by ammonia refrigerant under high adiabatic compression temperature. Using paraffinic or PAO lubricants can prevent carbon deposits and valves cokings.
References:
- ASHRAE Handbook, 1980 Systems. The American Society of Heating, Refrigeration and Air-Conditioning Engineers, Inc. 1980.
- Perry's Chemical Engineers' Handbook., 6th Ed. Robert Perry, Don Green. McGraw-Hill Inc., 1984
- Tribology Data Handbook. E. Richard Booser. CRC Press, 1997.
- Lubricants for Refrigeration and Air Conditioning, G Short and T. Rajewski. Lubrication Engineering, April 1995, P 270.