SHENZHEN DONGJIANG POWER PLANT COST ANALYSIS
A Full Showing How Steel Shield Saves The Operation Costs
Download the full report below:
1. Approach 1 – General Cost Reductions By Steel Shield
1.1. Lubricants: Low Cost, Big Impact
Buying low-quality lubricants can be a false economy. Lubricant costs are typically less than 5% of a power generation business’ total maintenance budget. We focus on providing performance products that can help to reduce maintenance requirements and increase reliability, and services that are designed to improve maintenance and business practices, and thus lower your overall costs.
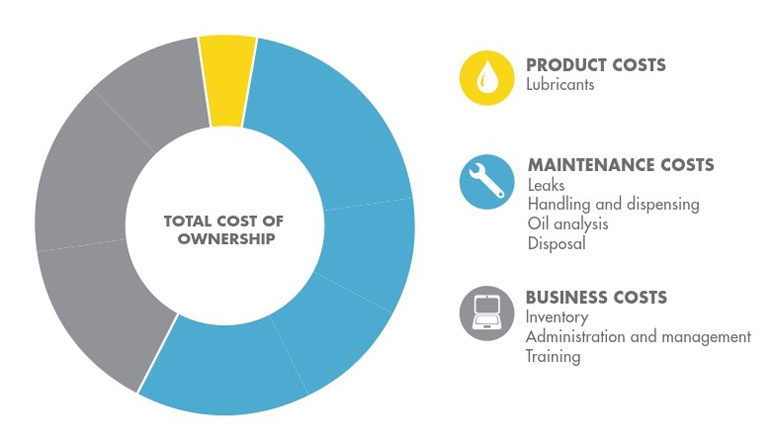
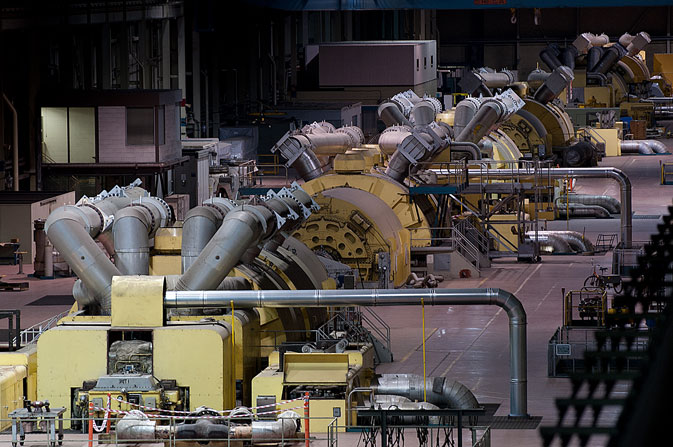
Fig 1. Total Cost of Power Plant Ownership
Fig 2. Gas Generator
1.2. Where Lubricants Can Add Value
Some examples of ways that lubricants can help your operation to run more efficiently:
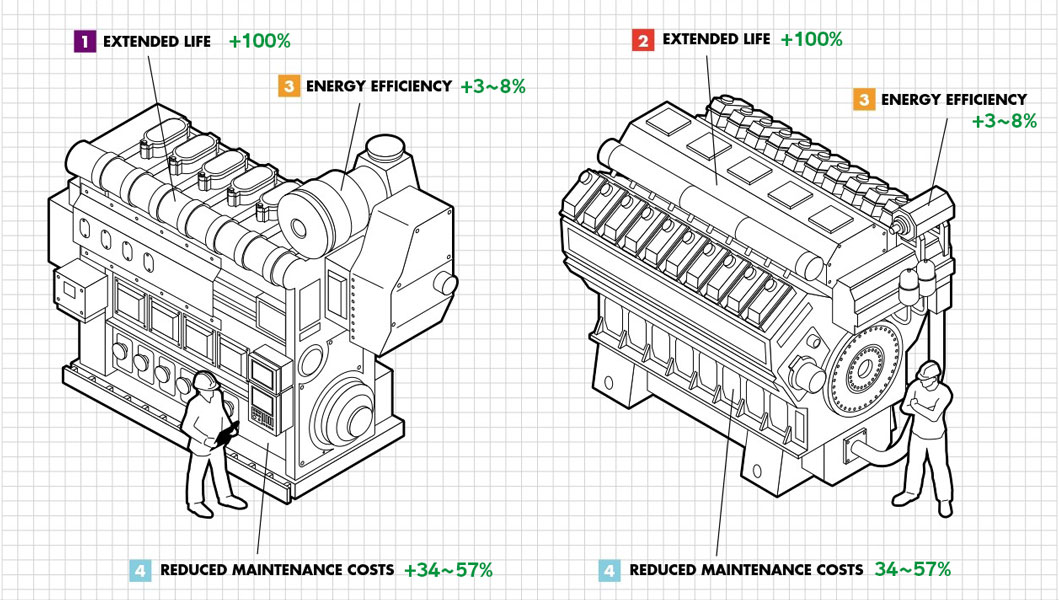
- According to the Total Cost of Ownership of Power Plant Generators (previous page), Lubricants Cost is about 5%, Maintenance Cost is about 55%.
- From the information provided by The Shenzhen Dongjiang Environmental Company Limited, it reveals that the total volume to purchase Caltex HDAX5500 LFG SAE40 lubricant is:
30 bottle x 200 liter x 12 times = 72,000 Litre
- The total cost to purchase Caltex HDAX5500 LFG SAE40 lubricant (tax included) is:
25 RMB/Liter x 72,000 Liter = 1,800,000.00 RMB
- The Total Cost of Ownership can be calculated as (with 5% lubricant cost):
1,800,000.00 RMB ÷ 5% = 36,000,000.00 RMB
- The total annual maintenance cost of Dongjiang is:
36,000,000.00 RMB x 55% = 19,800,000.00 RMB
- With the applications of Steel Shield lubricants, the yearly Maintenance Cost of machines can be reduced by 34% to 57%, which means:
6,732,000 RMB to 11,286,000.00 RMB
- The percentage reduction in Total Cost of Ownership by Steel Shield lubricants (%)
`(sf"Total Maintenance Cost Reduced"+sf"Lubricant Cost Reduced")/sf"Present Total Cost of Ownership"xx100%`
- ** Minimum =
`(6,732,000+1,440,580sf" (Note: Steel Shield No.3 Gas Engine Oil vs Caltex)")/(36,000,000)xx100%`=22.7% - ** Maximum =
`(11,286,000+11,332,904sf" (Note: Steel Shield No.3 Gas Engine Oil vs Caltex)")/(36,000,000)xx100%`=62.83%
2. Approach 2 – Cost Analysis Of Dongjiang Power Plant By Steel Shield
2.1. Basic Data of Qing Shui He Xia Ping Biogas Power Plant
Generator Data | ||||
---|---|---|---|---|
No. | Model | Quantity | Power (kW) | Total Power (kW) |
M1 | J320GSB 21 (GE Jenbacher) | 1 | 1063 | 1063 |
M1 | J320GSC 21 (GE Jenbacher) | 8 | 1063 | 8504 |
M3 | J320GSC 121 (GE Jenbacher) | 3 | 1063 | 3189 |
M4 | G3615 (Caterpillar) | 2 | 800 | 1600 |
Present Operation Data | ||||
---|---|---|---|---|
Lubricant Consumption | 6000 | litre / month | ||
Lubricant Refill | 1 | times / month | 12 | times / year |
Idle Time Before the Next MAJOR Maintenance | 6000 | hr | ||
Idle Time Before the Next Regular Maintenance | 2000 | to | 4000 | hr |
Duration of Maintenance (Each Machine) | 3 | to | 5 | days |
Downtime Cost (Each Machine) | 18000 | RMB / day | ||
Maintenance & Parts Cost (Entire Plant) | A | RMB / year |
2.1.1. Explanations
- Qing Shui He Xia Ping Biogas Power Plant have 4 types of generators with No. M1, M2, M3 and M4.
- The routine used lubricants analysis is about 200 hours for the first time (for new lubricants), and then 500 hours for the second time.
- The downtime cost includes the revenue lost due to the suspension of electricity generations.
- MAJOR Maintenance is the full functional examinations of generators. It is not included in the current cost analysis (for reference only).
- The variable “A” is a real number, it is used to make assumptions for Maintenance & Part Cost because this cost is not provided by the Qing Shui He Xia Ping Biogas Power Plant.
2.2. Improved Data by Steel Shield Lubricants
The Improved Maintenance Cost With the Application of Steel Shield | ||||
---|---|---|---|---|
Idle Time Before the Next Regular Maintenance (after refilled 2~5 times) | 4000 | to | 6000 | hr |
Reduction in Lubricants Refills (%) | 33 | to | 50 | % |
Lubricant Refill | 8 | to | 6 | times / year |
Parts Life Extended 2 Times and More, Maintenance Reduction (%) | 50 | % | ||
Maintenance & Part Costs (Entire Power Plant) | 0.5 | A | RMB / year |
2.2.1. Explanations
With Steel Shield lubricants, the following data can be improved:
- The Idle Time Before the Next Regular Maintenance: after Steel Shield is refilled 2 to 5 times, it is expected that the idle time can be extended from 4000 to 6000 hours.
- The Lubricant Refill times can be reduced from 8 to 6 times annually.
- The Maintenance & Part Costs can be dramatically decreased to 0.5A (only 50% of the original cost) annually (where A is a real number) due to the extended components life by ABF Technology of Steel Shield lubricants.
Other possible cost reductions by the application of Steel Shield but not included in the current calculation:
- Labor cost reduction: due to the reduction of unnecessary maintenance, reductions in overtime payments and reduction in employing temporary staffs.
2.3. Equations
Equations |
---|
Total Lubricant Cost = Lubricant Cost (RMB/Litre) X Lubricant Consumption (litre/Month) X Lubricant Renew (Times/Year)
|
Power Generator Maintenance Cost= Duration Per Maintenance (day) x Downtime Cost (RMB) x 365 days x 24 hr / Idle Time For The Next Regular Maintenance (hr) Example: To calculate the Minimum Maintenance Cost of Caltex, the maximum Idle Time for the Next Regular Maintenance (i.e. 4000 hr) and the minimum Duration Per Maintenance (i.e. 3 days) must be used. Alternatively, the Maximum Maintenance Cost of Caltex is calculated be the minimum Idle Time for the Next Regular Maintenance (i.e. 2000 hr) and the maximum Duration Per Maintenance (i.e. 35 days). The same method is applied when the Caltex is replaced by Steel Shield. |
Total Cost (Minimum) = Total Lubricant Cost (Minimum) + Total Maintenance (Minimum) + Maintenance & Part Cost Total Cost (Maximum) = Total Lubricant Cost (Maximum) + Total Maintenance (Maximum) + Maintenance & Part Cost |
Assumption of the present Maintenance & Part Costs: Due to the absent of real data, the Maintenance & Part Costs is assumed to be 0 to 1,000,000 per year, and the analysis is performed by using these range of data discretely. Assumption of the present Maintenance & Part Costs When Steel Shield is applied: Normally, with the applications of Steel Shield, maintenance cost can be reduced by 30~65%. The minimum and maximum TOTAL COST are based on these assumptions, therefore, the change of TOTAL COST can be revealed when the Maintenance & Part Costs changes from 0 to 1,000,000 RMB. |
Total Cost Reduction (Minimum), % = Total Cost After Steel Shield Applied (Maximum) - Total Cost When Caltex Applied (Minimum) / Total Cost When Caltex Applied (Minimum) x 100% Total Cost Reduction (Maximum), % = Total Cost After Steel Shield Applied (Minimum) - Total Cost When Caltex Applied (Maximum) / Total Cost When Caltex Applied (Maximum) x 100% From the above equations, the minimum and maximum reductions of TOTAL COST after Steel Shield is applied can be calculated respectively (in %). |
2.4. Annual Cost Analysis
2.4.1. Explanations
- 1. Under the column “Assumption of the present Maintenance & Part Costs, A (RMB / yr)”, A is the assumed annual cost. For example, if the assumed annual cost is 200,000 RMB, then the annual TOTAL COST (minimum) of Caltex HDAX5500 LFG SAE40 is 23,779,640 RMB and the corresponding maximum TOTAL COST is 27,642,800 RMB.
For Steel Shield lubricants, it is expected that the Assumption of the present Maintenance & Part Costs can be reduced by half. Therefore, the “Assumption of the present Maintenance & Part Costs When Steel Shield is applied, 0.5A (RMB / yr)” is A/2.
For example, if the assumed annual cost is 200,000 RMB, then this cost is reduced by half which is only 100,000 RMB. The annual TOTAL COST (minimum) of SST ECI GECAT No.1 HD-AP Gas Engine Oil SAE 30/40 0.5% Ash is then 15,048,842 RMB and the corresponding maximum TOTAL COST is 21,319,509 RMB.
-
“The TOTAL COST Reduction (Minimum), %” and “The TOTAL COST Reduction (Maximum), %” columns are the expected percentage changes when Steel Shield is applied.
For example, in order to calculate “The TOTAL COST Reduction (Maximum), %” of SST ECI GECAT No.1 HD-AP Gas Engine Oil SAE 30/40 0.5% Ash if the “Assumption of the present Maintenance & Part Costs”, A is 1,000,000, the “TOTAL COST (Minimum)” of SST ECI GECAT No.1 HD-AP Gas Engine Oil SAE 30/40 0.5% Ash and the “TOTAL COST (Maximum)” of Caltex HDAX5500 LFG SAE40 should be used in the calculation. The detail is as follow:
The TOTAL COST Reduction (Maximum),%
=((Min.TOTAL COST of SST ECI GECAT No.1 HD-AP Gas Engine Oil SAE 30/40 0.5% Ash)-(Max.TOTAL COST of Caltex HDAX5500 LFG SAE40))/(Max.TOTAL COST of Caltex HDAX5500 LFG SAE40) x 100%
=(12,194,856-28,442,800)/28,442,800 x 100%
=57% Reduction
2.5. Power Plant Graphical Cost Analysis
3. Conclusion
Applying Steel Shield lubricants:
- The annual Lubricant Cost with Steel Shield can be reduced by 10.6 million RMB, which is a substantial savings of 51.7%.
- The annual Maintenance Cost can be as low as 1.2 million RMB, which is 80% of the original.
- With the “Assumption of the present Maintenance & Part Costs”, the minimum TOTAL COST can be reduced to 11.7 million RMB, which is a COST SAVINGS of 59%.
- STEEL SHIELD comparing to the other make of lubricants can help reducing projected maintenance costs dramatically.