HOW TO CHOOSE THE RIGHT GREASE
A common OEM grease specification might be to use an NLGI No. 2 lithium grease of good quality. Using this information alone, one could select the right consistency and thickener type. Other considerations include thickener concentration, consistency, dropping point and operating temperature range, worked stability, oxidation stability, wear resistance, etc.
Base Oil Viscosity
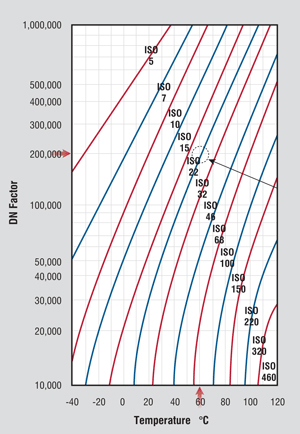
Figure. 1: DN Factor
Ref.: Stephen Sumerlin, Noria Corporation
A common mistake when selecting a grease is to confuse the grease consistency with the base oil viscosity. Because the majority of grease-lubricated applications are element bearings, one should consider viscosity selection for those applications. While most would not use an EP 220 gear oil for an oil-lubricated electric motor bearing, many people will use a grease containing that same oil for an identical grease-lubricated bearing. To determine minimum and optimum viscosity requirements for element bearings, one may use speed factors, commonly denoted as DN or NDm. Speed factors account for the surface speed of the bearing elements and are determined by the following formulas:
`D_n= sf"rpm" xx sf"bearing bore"`
`DN_m= sf"rpm" xx (sf"bearing bore"+sf"outside diameter")/2`
The NDm value uses pitch diameter rather than bore diameter because not all bearings of a given bore have the same element diameter, and thus have different surface speeds. Knowing the speed factor value and likely operating temperature, the minimum viscosity requirement can be read directly from charts like Figure 1.
Figure. 1 assumes the base oils’ viscosity index. To be more precise, one would need to use a chart that identifies the viscosity at operating temperature, then determine the viscosity grade from a viscosity / temperature chart for a given lubricant.
Additives And Base Oil Type
Table. 1 shows some common additive requirements by application. Most greases are formulated using API Group I and II mineral oil base stocks, which are appropriate for most applications. However, there are applications that might benefit from the use of a synthetic base oil. Such applications include high or low operating temperatures, a wide ambient temperature range, or any application where extended re-lubrication intervals are desired.
Additive | Journal Bearings | Ball Bearings | Thrust Bearings | Roller Bearings | Needle Bearings |
---|---|---|---|---|---|
Antioxidants | ✓ | ✓ | ✓ | ✓ | ✓ |
Antifoam Agents | ✓ | ✓ | ✓ | ✓ | ✓ |
Antiwear/EP | ✓ | ✓ | ✓ | ✓ | |
Rust Inhibitors | ✓ | ✓ | ✓ | ✓ | ✩ |
Extreme Pressure | ✩ | ✩ | |||
Demulsibility | ✓ | ✓ | ✓ | ✓ | ✩ |
VI Improvers | ✩ | ✩ | ✩ | ✩ | ✓ |
Corrosion Inhibitors | ✓ | ✓ | ✓ | ✓ | ✓ |
Table. 1: Lubricant additives requirements by application
✓: Required; ✩: Depends on application
Grease Consistency And Thickener Type
The NLGI has established a scale to indicate grease consistency which ranges from grades 000 (semifluid) to 6 (block grease). The most common NLGI grade is two and is recommended for most applications.
For bearings, speed factor and operating temperature can be used to determine the best consistency or NLGI grade for a given application. It may seem counterintuitive, but higher speed factors require higher consistency greases. Table. 2 provides a general guide to selecting NLGI grade based on speed factor and operating temperature.
Numerous types of grease thickeners are currently in use, the most common types are simple lithium soaps, lithium complex and polyurea. Simple lithium soaps are often used in general-purpose greases and perform relatively well in most performance categories at moderate temperatures. Complex greases such as lithium complex provide improved performance particularly at higher operating temperatures. A common upper operating temperature limit for a simple lithium grease might be 250℉, while that for a lithium complex grease might be 350℉. Another thickener type that is becoming more popular is polyurea. Like lithium complex, polyurea has good high-temperature performance as well as high oxidation stability and bleed resistance. Thickener type should be selected based on performance requirements as well as compatibility when considering changing product types.
Operating Temperature | DN (Speed Factor) | NLGI No.✸ |
---|---|---|
-30 to 100℉ |
0 - 75,000 75,00 - 150,000 150,000 - 300,000 |
1 2 2 |
-0 to 150℉ |
0 - 75,000 75,00 - 150,000 150,000 - 300,000 |
2 2 3 |
100 to 275℉ |
0 - 75,000 75,00 - 150,000 150,000 - 300,000 |
2 3 3 |
Table. 2: Grease NLGI grade selection guide
✸: Depends on other factors as well, including bearing type, thickener type, base oil viscosity and base oil type
Performance Properties
If an application operates continuously at room temperature, properties like dropping and upper operating temperature limits are not as important. If an application operates under heavy loads at low speeds, load carrying tests such as four-ball EP or Timken OK load should be considered. It is also important to review these specifications on a periodic basis to guard against specification creep. While improving a lubrication program can be a tough job, lubricant specification is relatively easy. Armed with a little bit of knowledge and a few widely available tools, it is possible to rest easier knowing that the right grease is being used.
With Steel Shield ABF Technology, the performance in stability, lubricity and interval of grease can be enhanced and improved to a much higher level.